3D Systems SLS 380
- Home
- Shop
- 3D printer, 3D Systems 3D Printer
- 3D Systems SLS 380
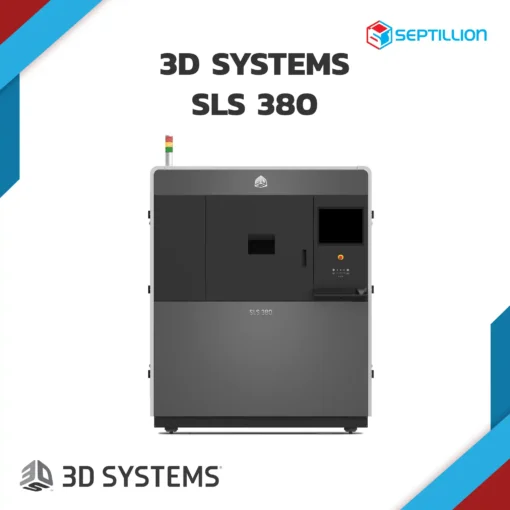
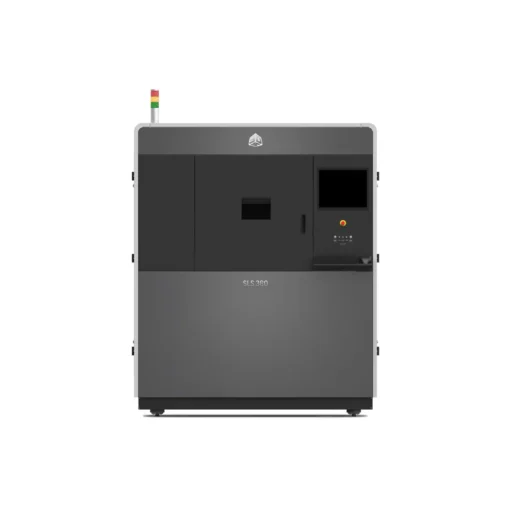
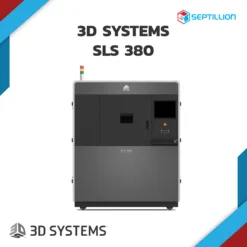
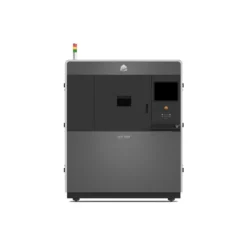
3D Systems SLS 380
Is a high-performance 3D printer utilizing Selective Laser Sintering (SLS) technology to produce precise and durable parts from a variety of materials. With a build volume of 381 x 330 x 460 mm (15 x 13 x 18 in), it delivers fast production speeds of up to 2.7 liters per hour. The printer is equipped with 3D Sprint® software for streamlined production control, fully automated powder handling, and optional 3D Connect for enhanced connectivity. Ideal for high-quality, large-scale manufacturing, the SLS 380 ensures consistent mechanical properties and maximized build volume for complex part production.
- Description
Description
3D Systems SLS 380 An industrial-grade SLS 3D printer
Enhanced printing capabilities for complex geometries
3D Systems SLS 380 is an advanced selective laser sintering 3D printer that excels in producing complex geometries and functional prototypes.
Its robust performance and reliability make it ideal for engineering, aerospace, and medical applications.
SLS 380 Guide PDF
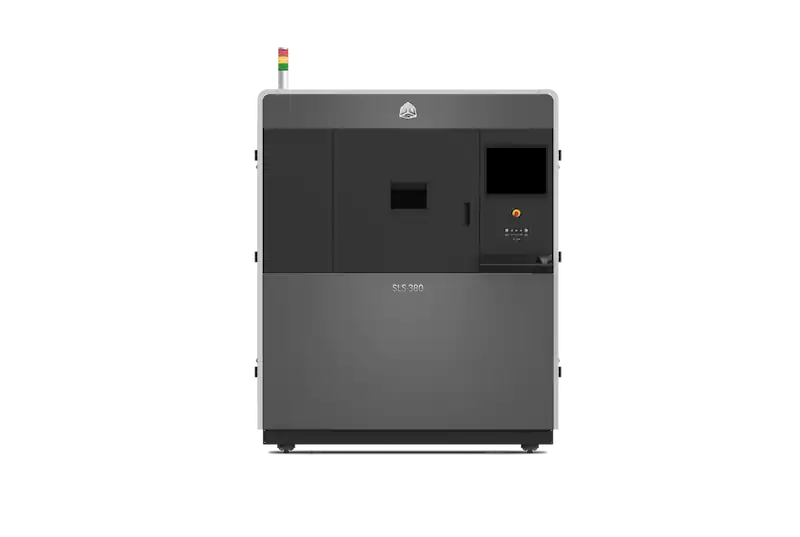
Production-Grade SLS Workflow Solution
The SLS 380 is a high throughput SLS additive manufacturing solution with unprecedented levels of throughput, consistency, performance, and yield. Optimized for those who want to take the next step in integrating additive manufacturing into their factory-floor ecosystem, 3D Systems’ SLS 380 and its complementary software, material handling, and post-processing solutions answer the demand for cost-effective batch production parts.
Repeatable Parts, High Yield
The SLS 380 features closed-loop process controls that enable high levels of repeatability across multiple parts, builds, machines, and sites. In addition to a new water-cooled laser, the system utilizes a custom-developed 3D Systems algorithm to manage, monitor, and control in real-time, the thermal uniformity within the build chamber.
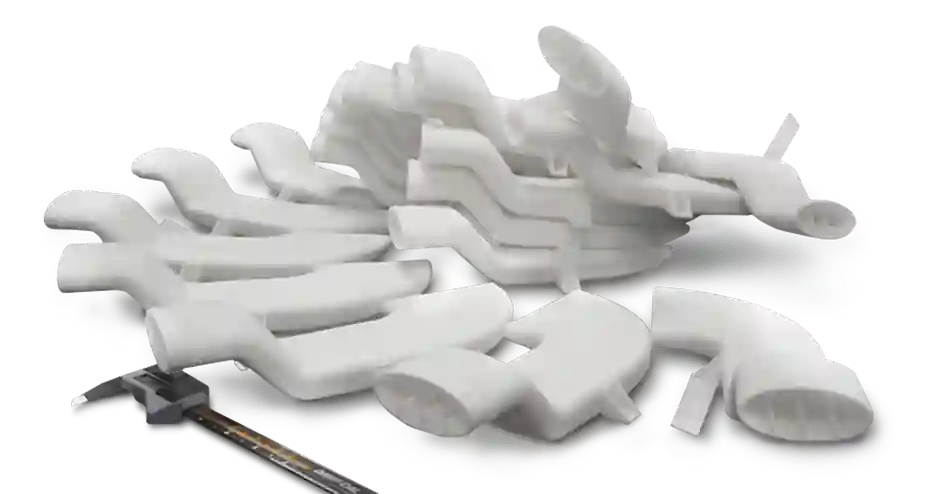
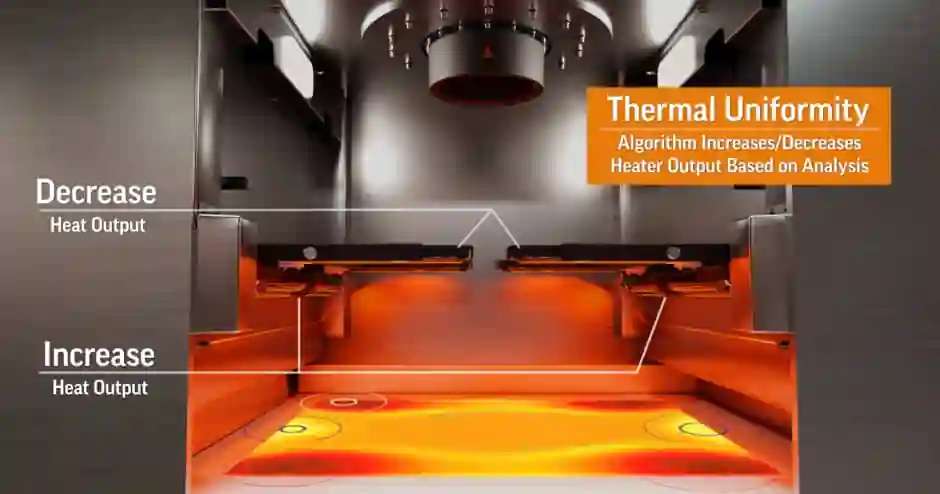
100,000 Thermal Data Samples Per Second
The algorithm manages eight separately calibrated heaters, together with an integrated high-resolution IR camera that captures over 100,000 thermal data samples from within the build chamber per second. This data, together with the IR sensor, maintains temperature stasis for every part build-layer, for the duration of the build process. With a more consistent thermal uniformity across the build process, manufacturers can now deliver more dimensionally stable parts with better mechanical performance, higher repeatability, and greater yields – all with fewer human interventions and lower overall operating costs.
Automate Material Handling
An important part of the SLS solution capability is the material quality center (or MQC) to control, blend, and deliver material on-demand for an optimal ratio of fresh and recycled powder. There are two MQC options for SLS printers: the MQC Single and the MQC Flex. The MQC Single is designed to connect to one SLS printer, whereas the MQC Flex is optimized to deliver material to up to four printers simultaneously, minimizing waste and eliminating operator intervention. The MQC Flex automatically blends fresh and recycled powder according to your specified mix ratio, and includes a recycled powder bin that provides convenient and immediate storage for unused powder post-printing. Both versions of the MQC feature fully-automated material feeding and an integrated breakout station for post-processing.
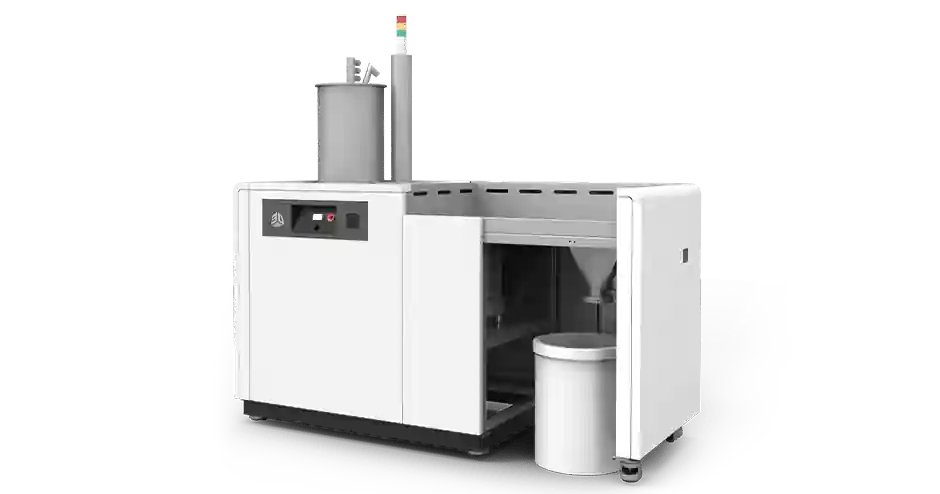
Tech Specs
- Selective laser sintering (SLS) technology
- Max build envelope capacity (W x D x H): 15 x 13 x 18 in (381 x 330 x 460 mm)
- Consistent mechanical properties
- High production speed for its class of 2.7 l/hr
- Streamlined production control, including 3D Sprint® integrated additive manufacturing software, fully automated powder handling and optional 3D Connect capability
- Automated 3D part nesting
- Maximized build volume and density